The diversity and magnitude of the many different types of systems, sub-systems, machinery utilized in large scale manufacturing plants of all types call for systemic and comprehensive solutions. The sheer diversity of resource use, their associated distribution systems, of course electricity demand and load characteristics, all necessitate analysis and identification of savings and improvement opportunities in deep and comprehensive manners.
Characterizing and designing solutions for the consumption patterns of many resources and systems simultaneously combines technical data, a variety of technologies, know-how gleaned from experience in industrial power optimization methods, and collaborative information sharing about your operations and processes. The combination of sound engineering grounded in data from your facility, and cost-benefit analysis of multi-faceted, integrated solutions is paramount.
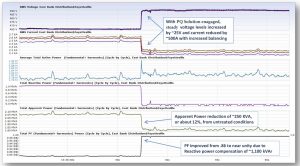
Due to widely varying and dynamic load conditions, manufacturing facilities have rapidly changing and dynamic power requirements. Supply insufficiency or failure of any resource – electricity, natural gas or other fuel, compressed air, water, steam – during a production cycle can cause enormous physical damage to both the product and equipment, production slow downs, and many other phenomena.
Furthermore, energy and resources that are wasted, distorted, unstable and/or are being supplied in less than optimal states to the loads and systems that consume them, are incurring expenditures that eat into operational profitability.
Solutions
Every sub-system in operation, whether part of the production process or integral to facility infrastructure, sometimes both, will be assessed. In each one, known ways in which power and resources are wasted, distorted, or inconsistent can be addressed with products and technologies that allow them to provide more output with less energy input. The results will manifest themselves in immediate bottom line savings on utilities – electric kWh costs, water and sewer costs, fuel bills, etc; cooler operations; increased production capability; significantly lower maintenance, repair and replacement time and expenditures; longer equipment life, expanded electric capacity; and more.
More cooling capacity can be obtained from your chilling systems with less power. Motor loads can be provided with the torque they need through real time power quality management (Volt VAR technology), smoothing demand spikes, eliminating distortions, improving run time conditions, all of which reduce costs. Lighting controls can dramatically enhance power used and quality of light. The opportunities for savings are too numerous to enumerate all of them.
The recommended solutions and technologies that will be deployed in a specific facility will take into account the technical, operational, and financial priorities and requirements of your business. Safety code and protocol will be taken into consideration as well. Many product families and technologies will typically be combined into an overall energy optimization solution at a specific location with specific operations. Identification of the most beneficial, and cost-effective treatments for specific production and/or infrastructural systems is part of the in-depth analysis and engineering process.
More information about our solutions for a variety of sub-systems, and how they can provide dramatic benefits to manufacturing facilities in myriad industries can be found on our Systems page.