Boilers, burners, engines, and generators all have a combustion process as the fundamental process of creating heat from matter. The matter in this case includes carbon based fuels – Natural Gas, Propane, Fuel Oil, Gasoline, Diesel of varying grades of refinement. Applications include hot water heaters , boilers for interior building heat using air or water, generators, industrial dryers, and vehicle engines of all sizes and types. There may be specialized burners as part of the production process as well.
Regardless of whether the fuel burning systems are aging or new efficient units, a gasoline vehicle or a newer diesel powered truck or bus, the combustion process can be made more efficient. One of the ways to make all of these combustion processes more efficient is to get more energy out of the fuel itself, while reducing emissions as well!
Combustion Burners and Engines
A very clever technology that has wide application in all of these systems involves passing the fuel through turbulent, repeated surface contact with conductive metal. The fuels retain a heightened electrostatic charge upon reaching the burn process. The observed vapor pressure will increase. The resulting spray pattern is better atomized and dispersed due to the electrostatic forces. Bottom line – More heat per unit of liquid/gas fuel and vastly reduced emissions!
The ECO System Fuel Enhancer is manufactured in many sizes, with a variety of installation kits to fit all boilers and vehicles. School districts with hundreds of busses, commercial trucking fleets, transport and worksite vehicles all benefit greatly. The same is true for industrial furnaces, boilers, and generators.
Diesel engine regen time and frequency is dramatically reduced as well.
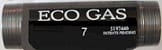
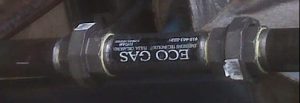
Steam and Condensate Handling Systems
For steam systems, in addition to getting more energy output from the fuel used by the boiler, we can help improve the yield and functionality of your steam distribution and condensate system, through high performance, longer lasting steam traps.
Our GEM Steam Traps work by using the difference in density between steam and condensate. Condensate is 1,000 times denser than steam and will pass through an orifice much slower than steam. The slow moving condensate squeezes out low density steam as it approaches the orifice. The high density, slow moving condensate is then preferentially discharged through the orifice, trapping the low density steam behind. The patented “venturi” orifice regulates condensate capacity over the full range of operating conditions.
- Energy savings of 10% to 30% permanent reduction in steam costs
- 10 Year No-Fail Performance Guarantee Excellent return on investment
- Simple paybacks typically range between 1 and 2 years
- 10 Year No-Fail Performance Guarantee
- Significant operational benefits from avoided repair/maintenance costs.
Consistent condensate discharge in changing load conditions, better retention of heat, and no moving parts!