Water Systems Analysis
The original Morrison Assisted Living facility in Whitefield, NH was constructed in 1904. Several additional wings have been added over the years. The current building is a modern, multi-purpose facility of 64,000 sq ft,. and 4 stories, with space for 80 residents.
Working together with The Morrison, a phased approach towards investments in operational energy efficiency was put in place. Installation of high efficiency, high lumen output LED lighting throughout the building was completed in the fall of 2019. Attention then turned to the water and heating systems. Implementation was scheduled for spring of 2020, though will now begin in the fall. Information here presents a case study of the assessment and analysis performed – the main focus points and results of the analysis of these systems and the recommended solutions, and projected results and benefits.
Description
The entire building is heated with a closed loop, forced hot water distribution system. The water heating is done by a bank of 8 boilers burning Fuel Oil #2, all connected into the main water distribution infrastructure, and sharing common exhaust manifolds. Thus, fuel oil bills are a significant part of the utility overhead expenditure, considering mean weekly consumption on the order of ~3000 gallons weekly.
Water quality was also a concern. Not only are health and sanitation standards of utmost importance, but thermal properties as well. Dirty and/or inconsistent quality of water affects pressure consistency in different parts of the system; reduces the heat exchange properties which wastes energy; causes dirt and scale buildup on valves, conduits, and sensors, leading to high maintenance and replacement costs. Such instances were reported as frequent and expensive.
As is typical of a resident facility, domestic hot and cold water consumption represents another major area of expense, with both water and sewer bills contributing. Weekly water consumption was on the order of ~4500 gallons weekly.
Technical and operational details were gathered and reviewed – piping sizes and layout, pressure and temperature specifications of the system, size and type of separators, seasonal patterns, etc.
Objectives of Engineering Analysis
- Identify ECMs (Energy Conservation Measures) and associated technologies which will –
- Reduce Heating System Water Consumption and Costs
- Reduce Domestic Water Consumption ands Costs
- Improve Heating Water System Water Quality
- Reduce Fuel Oil #2 Consumption and Costs, lowering emissions as well.
- Improve facility wide quality of heating throughout facility.
Results of Engineering and Solutions:
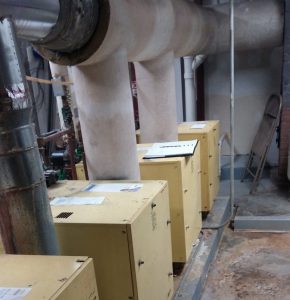
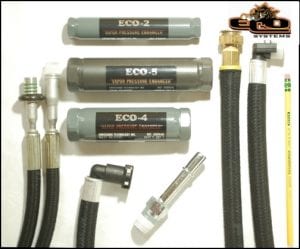
Solution: Improve Burn Efficiency of Fuel Oil
Fuel Savings: 8% – 12% Fuel Use Decrease
Cost Savings: $3396 – $5660 Annually
Projected Payback: 13 – 22 months
Product: ECOSystem Fuel Enhancers at Fuel Lines
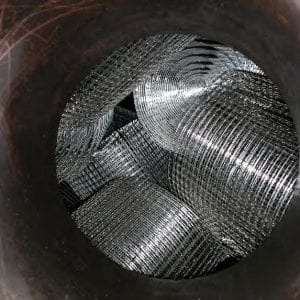
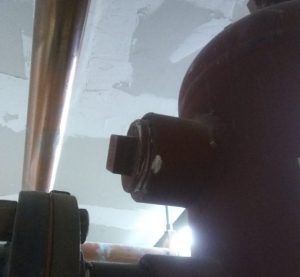
Solution: High Performance Air and Dirt Separator
Fuel Savings: 10% – 15% Fuel Use Decrease
Cost Savings: $4080 – $6120 Annually
Projected Payback: 7 – 11 months
Product: SweepClear Media Hydronic Water Filter
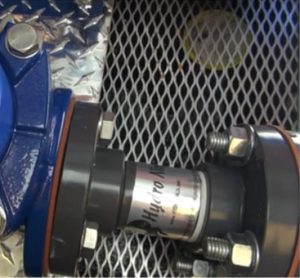
Solution: Improve Water Quality Through Meter
Water Savings: 5% – 12%
Cost Savings: $1269 – $3045 Annually
Projected Payback: 10 – 23 months
Product: Hydro Ninja Industrial Water Pre-Processor
Additional Solutions were considered and assessed for feasibility, and cost-benefit analysis. For example, the potential for Heat Recovery from the Boiler exhaust manifolds was assessed. The above solutions were the most effective as an integrated set of solutions, taking into account the physical and technical characteristics of the facility’s operations, and the requirements, budgets, and priorities of the The Morrison.
More information about these, and all of our Water System Energy Savings Solutions and how they can provide dramatic benefits to facilities utilizing water intensive systems can be found on our Systems page.
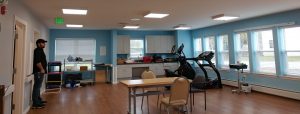